

Paul McClay wrote a reply on project log A word about Open Source and Patents.wooddragon48 has added a new log for Soldering Station for Milwaukee M18 Batteries.AIRPOCKET@rastaman vibration liked MEMOGRAM.wooddragon48 has updated the project titled Soldering Station for Milwaukee M18 Batteries.Aaron Lager has updated the log for OpAmp Buck Regulator.Yimin Rong on Ask Hackaday: Why Do Self Driving Cars Keep Causing Traffic Jams?.
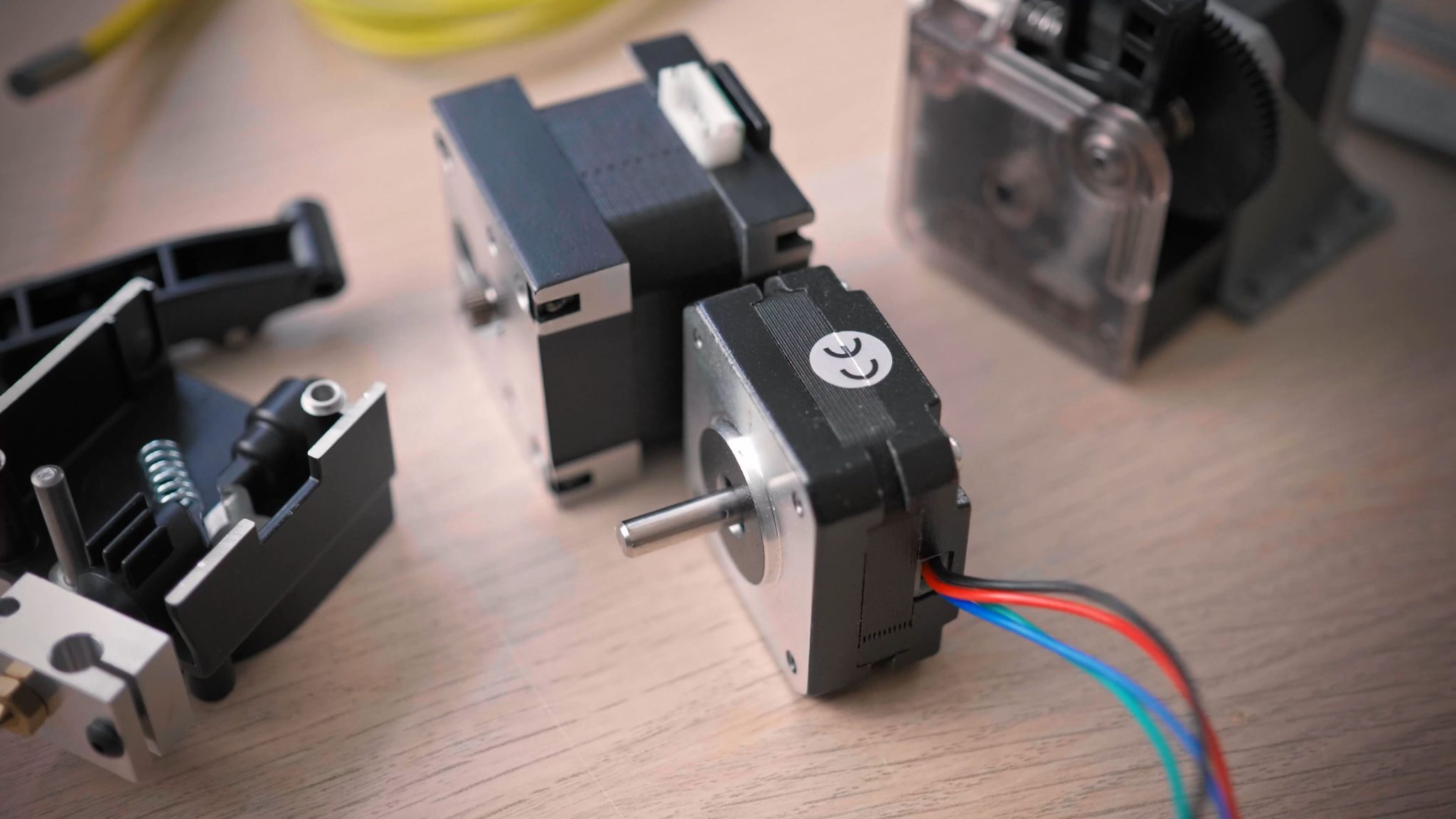
HEMERA 3D PRINTER SOFTWARE
Rapid iteration comes from a healthy library of software that can interact with the MCU. It is never worthwhile to cost optimize prototypes when the biggest value is rapid iteration. I do that all of the time with projects, the net result is they never get done or I end up on redoing it with the right equipment. In some applications, it just doesn’t make sense to optimize for price. Posted in 3d Printer hacks Tagged abs, diameter, filament, hall effect, magnet, PETG, PLA, quality control, sensor Post navigation
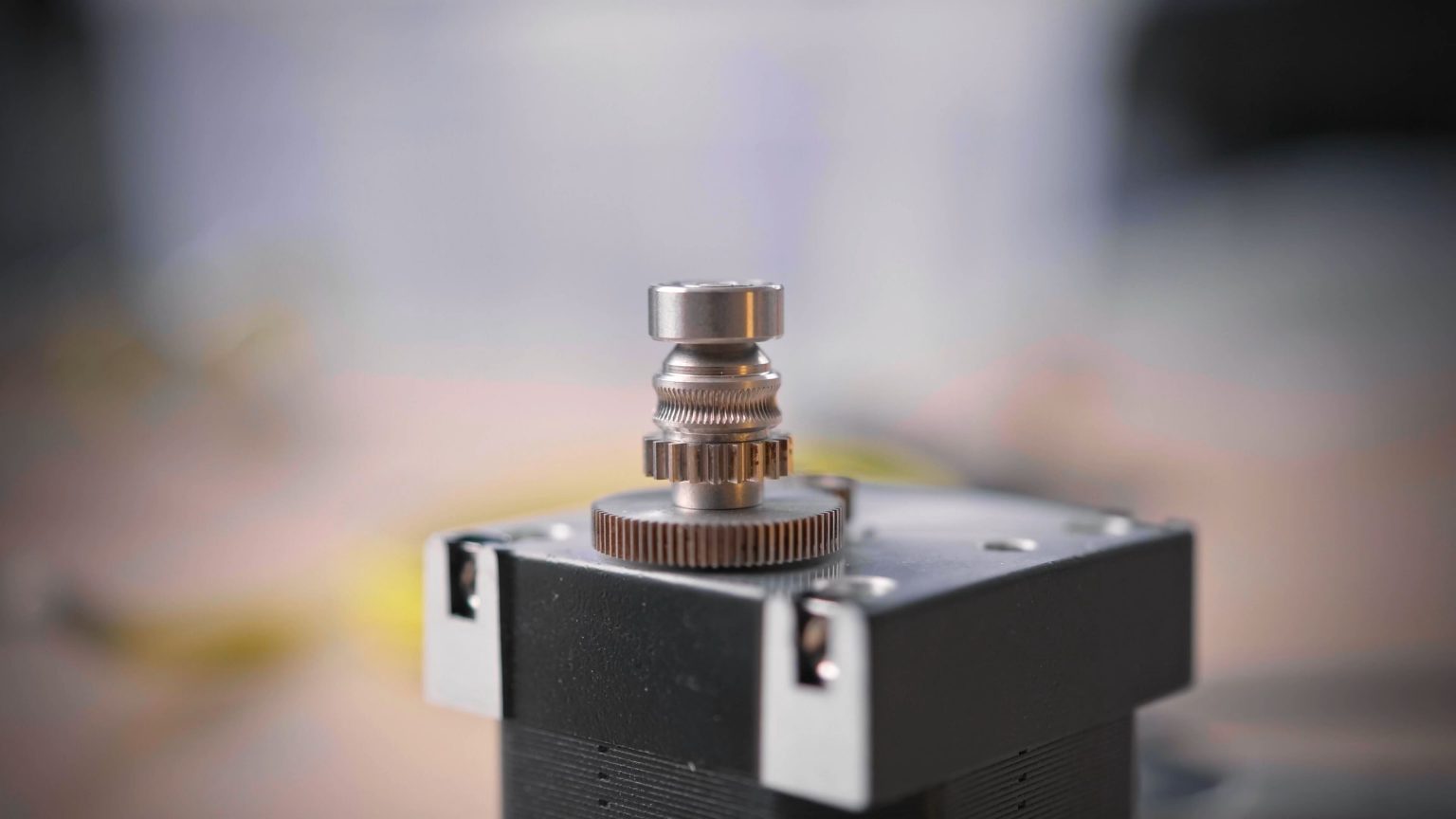
We’ve seen a few of those before, but this is a neat twist on that concept. When we see a filament sensor, it’s generally more of the “there/not there” variety to prevent a printer from blindly carrying on once the reel is spent. ran several different spools representing different manufacturers and materials through the machine we won’t spoil the results in the video below, but suffice it to say you probably have little to worry about if you buy from a reputable vendor.
HEMERA 3D PRINTER FULL
The full test rig has a motor-driven feed and takeup spools, and three sensors measuring across the filament in three different spots around the radius the measurements are averaged together to account for any small-scale irregularities. The lever is attached to a roller bearing that rides on the filament as it spools through the sensor variations in diameter are amplified by the lever arm, which wiggles a magnet over the Hall sensor, resulting in a signal proportional to filament diameter. Rather, used a very clever homemade device, which relies on a Hall effect sensor and a magnet on a lever to do the job. Those exist, but they are expensive bits of kit that are best left to the manufacturers, who use them on their production lines to make sure filament meets their specs. The heart of this build is not, as one might assume, some exotic laser device to measure the diameter of filament optically. Inquiring minds want to know, and when such minds are attached to handy fellows like, you end up with something like this home-brew filament measurement rig to gather the data you seek. Just how tight are the manufacturing tolerances of modern FDM printer filament.
